Introduction
Unit cost is a fundamental concept in business and economics. It influences many decisions related to production, pricing, and profitability analysis. It is more than just a numerical value; it helps you get insights that help with informed decision-making and strategic planning.
This article looks at the definition of unit cost and everything you need to know about it. From breaking down its key concepts and exploring its real-world applications, we take a deep dive into the larger scheme of things to help you understand its practical use for your organization.
So, without further ado, let’s look at how the cost of a unit plays a pivotal role in your organization’s expenses, production efficiencies, and pricing strategies.
Read About: Expense Management: The Ultimate Business Guide
What is the meaning of unit cost?
Unit cost is the price a business pays for each unit of a product or service when buying, selling, or storing it. Besides being crucial in shaping procurement strategies, it also helps forge mutually beneficial partnerships with your vendors. The metric holds the key to optimizing procurement decisions and negotiating contracts.
To understand the concept, let’s consider a scenario where a software startup seeks to purchase licenses for customer relationship management (CRM) software. The vendor offers a tiered pricing structure: INR 5000 per license for 1-100 requests, INR 4500 for 101-500, and INR 4000 for 501 and above.
In this case, the unit price would be the cost per license within each tier. If the software company decides to acquire 300 requests, the price of a unit for the first 100 licenses would be INR 5000 each, and for the following 200 licenses, it would be INR 4500 each.
Understanding these costs lets you strategically decide the number of licenses to purchase and which pricing tier to target. Ultimately, it will maximize cost savings while meeting your operational needs.
Read More: Strategic Procurement: What is it, Objectives, Process & Example
Why is unit cost essential in business?
Cost of unit plays is crucial in the strategic operations of businesses across industries. This metric can influence various aspects of business, from pricing strategies to profitability analysis. Let’s look at some reasons why it is crucial.
1. Pricing precision
Understanding the cost of the unit helps you set competitive yet profitable prices for your products and services. Knowing the direct costs of producing each unit will help avoid underpricing that erodes profitability or may drive customers away.
2. Efficient resource allocation
Knowledge of the cost of the unit will help you identify which products or services are more cost-effective to produce. You can focus resources on those areas, optimizing overall efficiency and resource utilization.
3. Informed decision-making
Cost of unit aids informed decision-making by evaluating the feasibility of launching new products and assessing the potential of outsourcing specific processes. A clear grasp of these costs provides valuable insights to guide strategic choices.
4. Performance evaluation
Monitoring changes in these costs over time allows you to evaluate the impact of process improvements and cost-reduction efforts in supply chain dynamics. It enables continuous refinement of operations and cost-saving initiatives.
5. Negotiation power
In B2B relationships, understanding the cost of a unit empowers you to negotiate better terms with suppliers. The knowledge of unit cost of production will help you confidently engage in contract negotiations and secure favorable pricing arrangements.
6. Profitability analysis
It is a vital aspect of profitability analysis. Comparing the cost of a unit with sales revenue helps ascertain which products or services contribute the most to your bottom line. You can confidently make decisions about resource allocation and product mix.
Must Read: 10 Best Expense Management Software and Tools
The formula for calculating unit cost
The formula for calculating the cost of the unit is as follows:
Unit Cost = Total Cost / Total Units Produced
In this formula, “total cost” is the costs incurred in the production process, including direct costs like raw materials, direct labor, and overhead expenses. “Total units produced” is the quantity of units manufactured or during a specific time.
To understand more details about this formula, consider a manufacturing company procuring raw materials from a supplier for their production line. Let’s say the total cost of purchasing 1,000 units of raw material is INR 15,000, inclusive of all expenses. Applying the formula, the price of the unit would be:
Unit Cost = INR 15,000 / 1,000 units = INR 15 per unit
Each unit of raw material purchased from the supplier costs the manufacturing company INR 15. Knowledge of this cost-of-unit figure helps assess the viability of the procurement deal. Besides negotiating better terms, you can make informed resource allocation and production planning decisions.
Types of unit costs
Understanding the various unit cost types is essential for a comprehensive grasp of cost analysis in business. The cost of the unit is of four types, each serving a unique purpose in financial evaluation and decision-making. Let’s delve into the intricacies of these types.
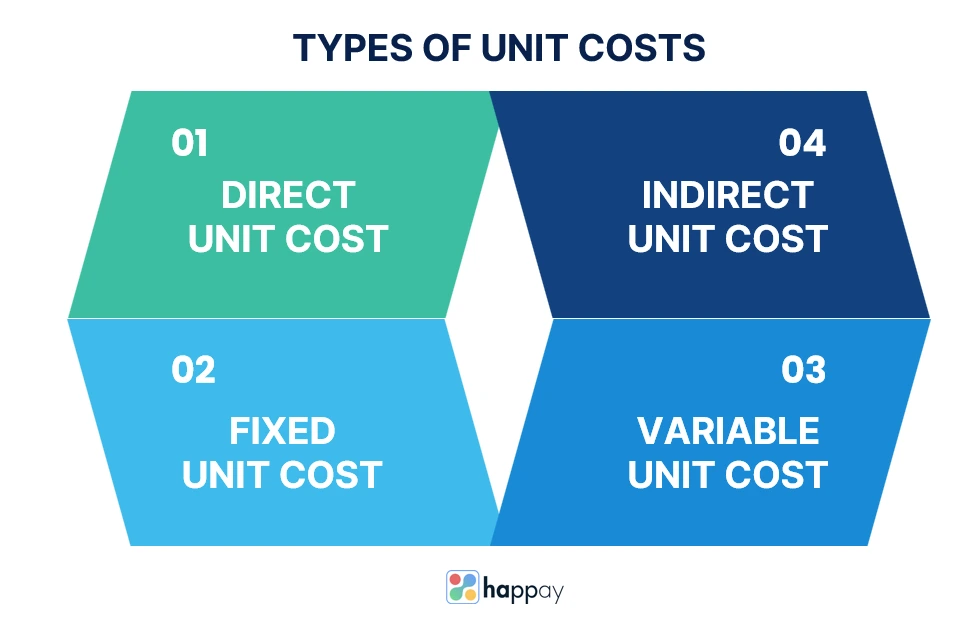
1. Direct cost of unit
The direct cost of a unit is the expenses directly attributed to the production or procurement of a specific unit of a product or service. For example, if an electronics manufacturer purchases microchips for its products, the direct cost of a unit would include the cost of each microchip.
Calculating the direct cost of a unit involves summing up all the direct costs associated with procuring or producing a unit and dividing by the total number of units procured or produced. If a software company procures 200 licenses of a specialized software solution for INR 10,00,000, the direct cost of a unit would be INR 10,00,000 ÷ 200 licenses = INR 5000 per license.
2. Indirect cost of unit
The indirect cost of a unit includes expenses not directly tied to a specific unit but contribute to the overall operational efficiency. For example, if a manufacturing company procures machinery, the maintenance and repair costs associated with the machinery will be indirect costs.
Calculating the indirect cost of a unit entails aggregating all indirect costs over a specific period and dividing by the total number of units procured or produced during that period. If a company’s annual administrative and facility costs amount to INR 10,00,000, and it procures 500 units of a product, the indirect cost of a unit would be INR 10,00,000 ÷ 500 units = INR 2000 per unit.
3. Fixed cost of unit
Fixed cost of unit denotes constant costs regardless of the quantity of units procured or produced. For example, if a logistics company leases a warehouse for storage, the lease cost would be a fixed cost of a unit.
Calculating fixed unit cost involves dividing the total fixed costs over a specific period by the total number of units procured or produced during that period. If a supplier’s annual fixed costs amount to INR 50,000 and supplies 10,000 units, the fixed unit cost would be INR 50,000 ÷ 10,000 units = INR 5 per unit.
4. Variable cost of unit
Variable cost includes costs that fluctuate based on the number of units procured or produced. For example, the direct material costs would be variable if a clothing retailer procures fabric for making garments.
Calculating a unit’s variable cost involves summing up all the variable expenses over a specific period and dividing by the total number of units procured or produced during that period. If a manufacturer procures raw materials for INR 3,00,000 and has 500 units, the variable cost of units would be INR 3,00,000 ÷ 500 units = INR 60 per unit.
Read About: Operating Cost: What is it, How to Monitor, Adjust & Calculate It?
Importance of unit cost analysis
Cost-of-unit analysis is critical as it offers profound insights into business operations, pricing strategies, and the financial health of an organization. Let’s look at why this analytical approach holds a lot of importance.
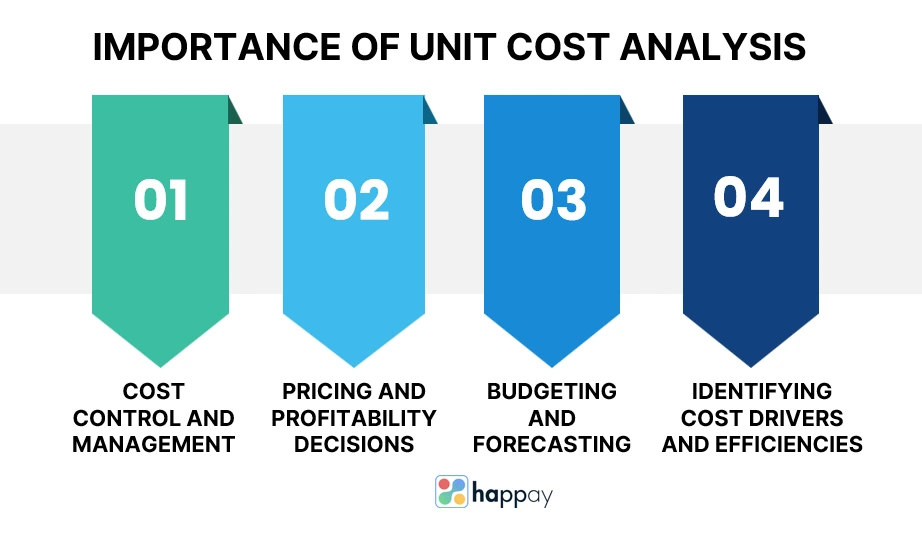
1. Cost control and management
The analysis provides an overview of the expenses associated with one unit of a particular product or service. The breakdown serves as a roadmap for cost control and management. It enables you to pinpoint areas for cost reduction and streamlining. A granular understanding of each cost component helps you make informed decisions to optimize your processes and allocate resources efficiently.
2. Pricing and profitability decisions
A thorough grasp of the costs incurred in producing each unit empowers you to set competitive prices and ensure healthy gross profit. Aligning pricing with the actual expenses helps avoid pricing your products too low or too high.
3. Budgeting and forecasting
Effective budgeting and forecasting hinge on accurate cost estimation. The analysis provides the foundation for creating realistic budgets and projections. It allows you to anticipate expenditures and revenue streams with greater precision. It fosters financial stability and aids in proactive resource allocation.
4. Identifying cost drivers and efficiencies
Unveiling the various components that contribute to the cost of a unit helps identify the key cost drivers within production. The insight enables you to target areas for cost reduction or process improvement. Understanding the impact of changes in input costs or production volume will help implement measures to enhance operational effectiveness.
How to calculate and analyze unit cost?
Calculating and analyzing unit cost is essential for understanding the cost efficiency of producing a particular item or offering a service. Here’s a basic guide:
- Gather cost data
Collect relevant cost data associated with the production or procurement of the product or service. It includes direct costs like materials and labor and indirect costs like overhead and administrative expenses.
- Identify the type of unit cost
Determine the type of cost of the unit you’re calculating – whether it’s direct, indirect, fixed, or variable. The distinction will guide your calculations and subsequent analysis.
- Calculate the total cost
Sum up all the relevant costs gathered in step one to calculate the total cost for the production or procurement period.
- Determine total units
Find out the total number of units produced or purchased during the same period.
- Apply the unit cost formula
Use the appropriate formula based on the type of unit cost for calculation. For direct unit cost, divide the total cost by the total units. The process remains similar but involves different cost components for indirect, fixed, or variable unit costs.
- Analyze and interpret the result
Once you have the overall unit cost value, delve into its implications. Compare it to historical data or industry benchmarks to gauge cost efficiency. Analyze trends over time to identify fluctuations and patterns. Additionally, assess how the cost of a unit aligns with pricing strategies and gross profit margins.
- Identify opportunities for improvement
Examine the components of the cost of the unit to pinpoint areas for improvement. Are there ways to reduce material costs? Is it possible to enhance operational efficiencies to lower labor expenses? Use this analysis to develop strategies for cost reduction and process optimization.
- Incorporate findings into decision-making
The insights gained from the analysis will help you make informed decisions. Adjust pricing strategies and streamline operations based on your findings.
- Continuously monitor and update
Unit cost analysis is an ongoing process. Regularly review and update your calculations to reflect changes in cost structures and production volumes. The iterative approach ensures your decision-making remains aligned with market realities.
Read About: TOP 10 Procurement Software Solutions
What is an example of a cost unit?
Let’s explore an example to understand the concept better. We will look at the case of packaging material for an electronics manufacturer.
Consider an electronics manufacturing company in India that specializes in producing smart devices. The company sources packaging materials for its products from a supplier. The cost unit here could be a “packaging unit.” A packaging unit could contain a specific type and quantity of materials required to package one electronic device for shipping.
Consider that the packaging materials include a cardboard box, protective foam, and a printed instruction manual. The cost of procuring these materials, including manufacturing and shipping, is INR 100 per packaging unit. For every electronic device produced and packaged, the cost associated with packaging is INR 100.
The electronics manufacturer can analyze and compare the packaging costs for different product lines using a cost unit. It can assess whether specific packaging designs are more cost-effective or explore options for bulk purchasing to reduce costs. The analysis empowers the manufacturer to make strategic decisions aligning with cost efficiency and profitability.
Factors affecting the unit cost
Unit cost can be influenced by many factors that shape cost structures and operational efficiencies. Let’s explore them in detail.
1. Economies of scale
Economies of scale happen when the cost per unit decreases as production volume increases. When producing or procuring in larger quantities, fixed costs like machinery and equipment are spread over more units, leading to lower average costs. The phenomenon is especially evident in B2B scenarios, where bulk orders can lead to cost advantages.
2. Production volume and capacity utilization
Higher production volumes generally lead to lower unit costs due to spreading fixed costs. Moreover, maximizing capacity utilization ensures resources are used optimally. It minimizes idle time and reduces costs per unit.
3. Input prices and supplier relationships
For example, a rise in the raw materials cost can lead to an increase in the cost per unit. Strong supplier relationships can help negotiate favorable terms, stabilize prices, and secure discounts. All these factors ultimately influence the cost of a unit.
4. Process efficiency and technology
Efficient production processes driven by technology can substantially lower the cost of a unit. Automation, streamlined workflows, and lean practices reduce labor and time requirements for enhanced efficiency. Investments in innovative technologies can lead to cost savings over the long term.
Unit cost in different industries
Unit cost manifests uniquely across various industries, reflecting the intricacies and dynamics specific to each sector. Let’s explore how unit cost operates in a few distinct industries.
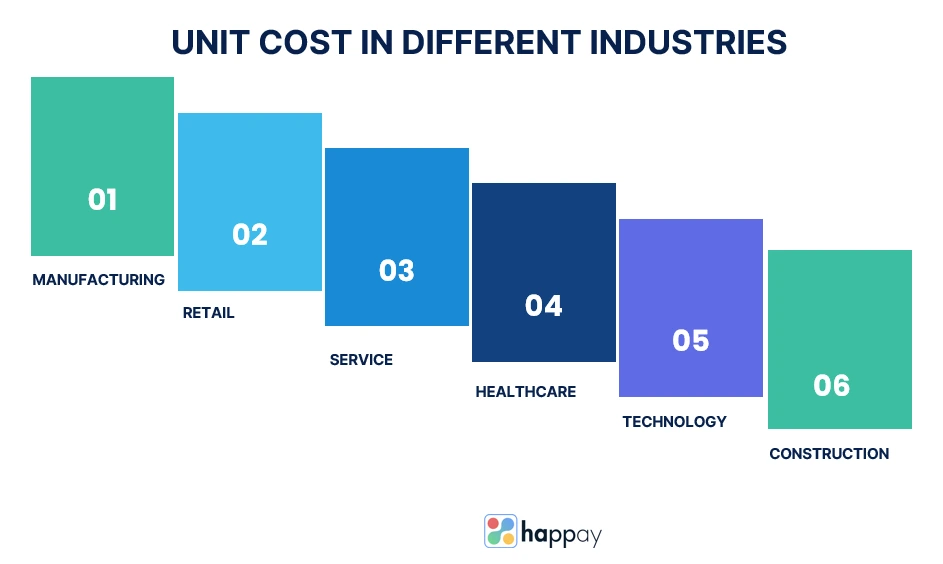
1. Manufacturing
In manufacturing, the cost of a unit helps assess production efficiency. It includes raw materials, direct labor, machinery, and other production-related expenses. Calculating the cost of units aids manufacturers in pricing strategies, optimizing production volumes, and identifying cost-saving opportunities.
2. Retail
For retailers, the unit cost is the expense of procuring products for resale. It includes the cost of goods purchased from suppliers, shipping, handling, and potential markups. Unit cost guides pricing decisions to ensure competitive yet profitable pricing structures for the better financial health of retailers.
3. Service
In the service sector, the cost of a unit translates into the price of delivering a single service. It includes employee wages, time spent, and overhead costs related to service provision. Understanding the cost of a unit assists service providers in evaluating service packages and setting pricing.
4. Healthcare
In healthcare, the cost of a unit takes on the dimension of providing medical care. It includes expenses tied to patient treatment, including personnel, medical supplies, facility maintenance, and administrative costs. The cost of unit analysis helps healthcare institutions balance quality patient care with financial sustainability.
5. Technology
The technology sector involves the production or procurement of technology products, from software licenses to hardware components. For example, in software development, the cost analysis factors in coding time, testing efforts, and potential licensing fees. Understanding these costs is essential for product pricing and profitability assessment.
6. Construction
For construction companies, the cost of a unit covers everything from materials to direct labor and equipment required for building projects. The cost assessment helps in project estimation, budgeting, and bidding strategies.
Learn About: CapEx vs. OpEx: A Guide to Understanding the Differences
Difference between unit cost and total cost
Let’s delve into the key differences between the two concepts.
Aspect |
Unit Cost |
Total Cost |
Definition |
The cost associated with producing a single unit of a product or service. |
The sum of all costs incurred in production or operation. |
Focus |
Focuses on the cost of individual units. |
Encompasses all costs, regardless of units. |
Calculation |
Calculated by dividing total cost by total units produced or purchased. |
Calculated by summing up all individual costs. |
Decision-Making |
Used for pricing strategies and cost control. |
Used for budgeting, financial planning, and decision-making. |
Comparative Analysis |
Compares costs per unit across different products or services. |
Compares overall costs across different time frames or projects. |
Impact of Scale |
Affected by economies of scale, it may decrease as production volume increases. |
Generally increases with production volume. |
Best practices for effective unit cost management
Effective management of the cost of the unit helps with prudent financial decision-making and operational excellence. Here are some best practices to guide you in effective control.
1. Detailed cost tracking
Maintain a comprehensive record of all production, procurement, and operational costs. It includes direct, indirect, fixed, and variable costs. Accurate cost tracking provides a solid foundation for the cost analysis process.
2. Regular analysis and review
Regularly review and update your calculations to reflect changes in input prices, production volumes, and market conditions. Timely analysis helps identify trends, anomalies, and areas for improvement.
3. Accurate allocation of costs
Ensure costs are allocated accurately to the appropriate units or products. Misallocation can lead to distorted insights and erroneous decision-making. Use precise cost allocation methods that align with your organization’s operations.
4. Benchmarking and industry comparisons
Benchmark your cost of the unit against industry standards and competitors. It provides insights into your cost competitiveness and highlights areas where you might need adjustments to remain competitive.
5. Consider economies of scale
Strategically leverage economies of scale by optimizing production volumes. Bulk purchasing and higher production quantities often lead to lower costs due to the spreading of fixed expenses.
6. Supplier collaboration
Develop strong relationships with suppliers. Effective supplier collaboration can lead to favorable terms, discounts, and stable pricing, influencing costs positively.
7. Process efficiency improvements
Focus on enhancing operational efficiency. Streamline processes, reduce waste, and explore technology-driven solutions to lower labor and time requirements.
8. Pricing strategy alignment
Ensure your pricing strategies remain aligned with the cost of a unit. Avoid underpricing, which can erode profitability, and overpricing, which can deter customers. Your pricing should reflect both cost realities and market demand.
9. Scenario analysis
Scenario analysis helps assess the impact of changes in variables like input prices, production volumes, and market demand on the cost of a unit. The proactive approach helps you plan for different eventualities.
Read About: Best Expense Tracking Software
Limitations and challenges of unit cost analysis
While the cost of unit analysis is a valuable tool for financial decision-making, it’s essential to recognize its limitations and challenges. Awareness of these constraints ensures you approach the analysis with a balanced perspective.
Here are some challenges to consider:
1. Simplification of costs
The analysis might oversimplify the complex nature of costs. It often aggregates various cost components into a single figure, ignoring nuances and intricacies within different cost categories.
2. Ignoring fixed costs
The analysis focuses on variable costs, potentially overlooking fixed costs that remain constant irrespective of production volume. Ignoring fixed costs can lead to incomplete insights.
3. Changing cost structures
The cost of a unit can change rapidly due to fluctuations in input prices, technological advancements, or shifts in market conditions. The dynamic nature requires continuous monitoring and adjustment.
4. Does not consider revenue
The analysis doesn’t directly consider revenue generation. A product with a low cost per unit might not be profitable if its sales price doesn’t cover other expenses and provides a reasonable gross profit margin.
5. Neglecting quality and value
Solely focusing on the cost of a unit could compromise product quality or perceived value. Cutting costs without considering quality implications can harm customer satisfaction and brand reputation.
6. Incomplete allocation methods
Allocating costs to specific units or products might involve assumptions that don’t accurately represent the actual consumption of resources. It can lead to skewed figures.
7. Difficulty in cross-industry comparisons
Comparing costs across different industries can be challenging due to variations in production processes, resource requirements, and market dynamics.
8. Limited in strategic decision-making
While valuable for short-term decisions, the analysis might not be sufficient for complex strategic choices that require a broader perspective and consideration of long-term implications.
9. Complexity in overhead allocation
Allocating indirect costs, particularly overhead, can be complex. Various methods exist, each with pros and cons, making choosing the most accurate approach challenging.
10. Doesn’t capture external factors
The analysis often focuses on internal factors within a business. It might not capture external factors like regulatory changes and macroeconomic shifts that can impact costs.
Read About: A Comprehensive Guide to Financial Management
Bottom line
Every decision carries financial implications for your organization. A deep comprehension of the cost of a unit thus emerges as a guiding light. It’s not just about crunching numbers; it’s about deciphering the intricate world of expenses that shape your organization’s operational landscape.
From setting prices that strike a balance between competitiveness and profitability to optimizing resource allocation, the cost of a unit can be an ultimate savior. Its accurate understanding is essential for steering through the complex web of financial decision-making. Remember, the price of a unit isn’t just a metric – it’s the key to unlocking informed and prudent financial choices.
FAQs
It is the expense incurred to produce or purchase a single unit of a product or service. The concept helps in understanding the cost structure associated with each unit.
To calculate the cost of a unit, divide the total cost (including relevant expenses) by the total number of units produced or purchased.
A cost unit is a specific measure that quantifies costs, like a single product, service, or activity. Conversely, cost refers to the monetary value spent on producing goods, providing services, or undertaking activities.
The cost per unit is the total cost divided by the number of units (1 unit). It represents the cost associated with producing or purchasing a single unit.
Cost-per-unit analysis is crucial for pricing strategies, profitability assessment, and resource allocation. It provides insights into the financial impact of producing or purchasing individual units.
Fixed cost per unit is the portion of fixed costs attributed to each unit produced. You can calculate it by dividing the total fixed costs by the total number of units.
The fixed cost formula is Fixed Cost = Total Fixed Costs. It represents all constant costs regardless of production or activity levels.
Profit per unit is the amount of money earned from selling one unit of a product or service after subtracting the cost of the unit from the selling price.
A unit variable cost is the cost that varies in direct proportion to the production or purchase of each unit. It includes expenses like raw materials and direct labor costs, which change as production levels change.
Discussion about this post