Introduction
A prime cost is directly incurred when an enterprise produces a good or service. Organizations can use these expenses to calculate the contribution margin. It helps determine the minimum price they should sell their products or services.
All businesses require prime cost analysis to understand the direct expenses of producing goods or services and set competitive pricing. Even service-based businesses can benefit from prime cost analysis when calculating the direct costs of delivering their services, enabling them to better manage and control costs.
Read More: What are Business Expenses: A Complete Guide
What is prime cost?
The prime cost is the sum of the direct costs for materials, labor, and expenses. Also known as direct cost or flat cost, companies estimate it by adding raw material costs, direct labor costs, and direct expenses.
It alludes to the expenses of producing products or services that maximize a company’s profit margin. Prime costs determine the direct costs of labor and raw materials used in manufacturing a good.
Direct costs do not include indirect costs such as advertising and administrative expenditures.
Quick Read: Capital Expenditure (CapEX): Meaning, Types, Examples & Formula
Importance of prime cost in business accounting
Businesses use these costs as a metric to calculate the total cost of the manufacturing inputs needed to produce an output. A company can raise its profit margin or undercut its rivals by reducing its such costs.
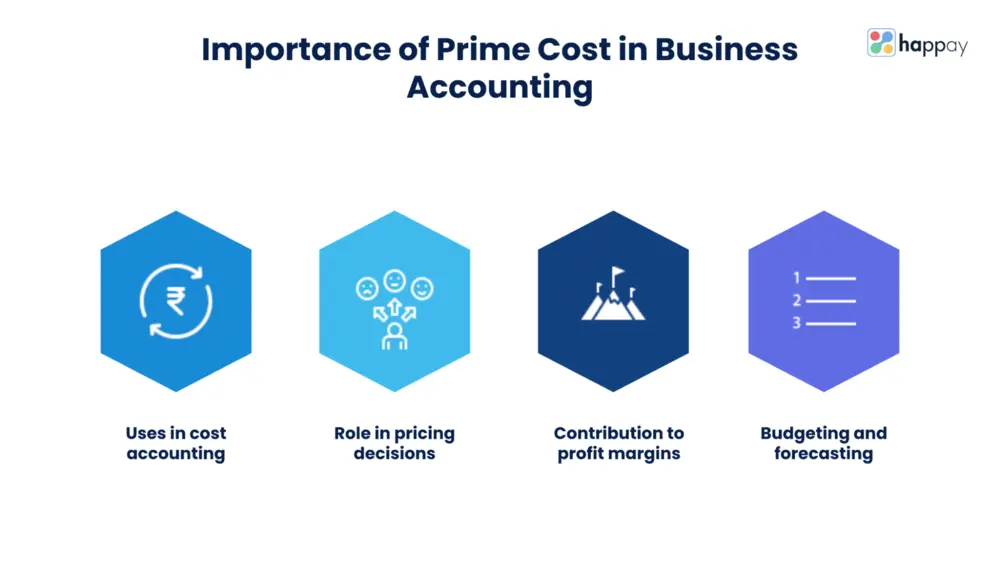
1. Use in cost accounting
In management and cost accounting, prime costs are essential to compute the contribution margin, establish pricing, forecast sales and profits, and facilitate decision-making. The approach entails calculating a product’s contribution margin, revealing its capacity to cover fixed expenses and profitability.
While the production of goods and services incurs various expenses, the formula focuses solely on variable expenses directly tied to the production of each item.
The formula is
Prime Costs = Raw Materials + Direct Labor.
2. Role in pricing decisions
You can set competitive prices to ensure profitability and sustainability by understanding the direct expenses incurred in producing goods or services. Here are two critical points on how this cost helps in pricing decisions:
- Cost-based pricing. Businesses determine the total production cost of each product unit. It allows them to add a suitable profit margin to cover overhead costs and generate desired profits.
- Competitor analysis. Companies identify areas of cost efficiency or potential cost reduction opportunities. If a business’s prime costs are significantly higher than its competitors, it may need to reassess its production processes, negotiate better deals, or optimize labor utilization. Conversely, if a company’s prime cost is lower than its competitors, it may have a competitive advantage.
3. Contribution to profit margins
The cost percentage represents a business’s prime cost divided by its sales, aiding in determining profit margins and identifying whether the costs of goods or labor are excessive.
Prime Cost Percentage = Prime Cost / Sales
4. Budgeting and forecasting
Budgeting and forecasting help in a company’s growth journey, especially during periods of change.
You can create budgets with a detailed breakdown of direct material costs, direct labor expenses, and other direct production costs, helping companies set realistic targets and allocate resources efficiently.
Forecasting salesperson’s predicted numbers and profits become more precise when integrated prime cost data allows businesses to anticipate revenue streams and identify potential cost fluctuations. It empowers companies to create comprehensive financial plans aligned with their production capabilities and market condition. It ensures better financial stability and performance over time.
Quick read: Operating Expenses (OpEx) – Meaning, Types & Formula
Role of prime cost in determining total production cost
Total production cost represents the cumulative expenses incurred by a business during its production operations within a specific reporting period.
There are two approaches to accounting for total production cost. The first one charge the entire cost as an expense in the reporting period. It aligns with the cost of goods sold and is suitable when meeting customer demand with minimal inventory buildup.
The second approach involves allocating a portion of the cost as an expense and assigning the rest to inventory on the balance sheet. It’s applicable when producing more goods than immediate customer demand requires, resulting in inventory accumulation.
The formula is Total product cost = Cost of raw materials + cost of direct labor + cost of overhead.
Quick read: Incidental Expense: Meaning, Types and Challenges
Components of prime cost
These costs consist of direct expenses directly linked to each unit of a manufactured product. These costs typically encompass three main components:
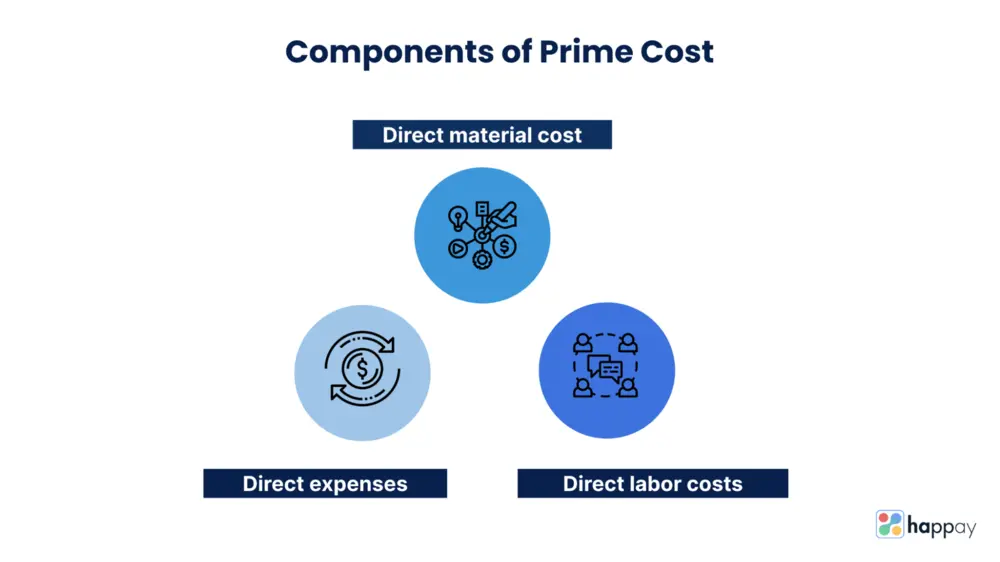
- Direct materials are tangible goods or supplies associated explicitly with a particular product. They include raw materials used in production that ultimately become finished goods.
- Direct labor includes workers or employees directly producing a specific product. These laborers apply their skills during manufacturing to create the final products.
- Direct Expenses are apart from material and labor costs. They’re a part of the prime cost, regardless of whether they are variable costs or sometimes semi-variable. Some companies take administrative costs or employee bonuses as a part of direct expenses.
Quick Read: SG&A Selling, General and Administrative Expenses
How to calculate prime cost?
Calculate direct material and labor costs to calculate the prime cost in your organization.
- Direct materials cost calculation
Direct materials costs encompass the expenses incurred for acquiring any raw material, component, or stock item utilized in the manufacturing process of a product.
To determine the cost of direct materials incurred during the period, sum up the total cost of materials purchases with the cost of beginning inventory and then subtract the ending inventory costs.
Below is the formula to calculate the cost.
Direct material cost = Opening direct material inventory + direct material purchased – closing direct material inventory - Calculation of direct labor cost
Direct labor cost encompasses the complete wages and benefits disbursed to the employees directly manufacturing the company’s products or providing its services.
It covers more than just employee wages. It contains various additional costs directly linked to the production process, such as payroll, taxes on employee wages, workers’ compensation insurance, life insurance, medical insurance, and other company-provided benefits.
Here’s the formula for calculation.
Direct labor cost = Pay rate * Time to complete a task or project. - Summing up costs to calculate prime cost
In manufacturing goods and services, various expenses come into play. However, the formula in question considers the variable expenses directly linked to each item’s production.
The prime cost is derived by summing up the cost of direct raw materials with the expenses of labor directly included in the production process.
Prime cost = Raw materials + direct labor
Learn more about: How to Choose the Right Expense Tracking Software?
Importance of prime cost analysis
Prime cost analysis is crucial in a company’s financial management and decision-making processes. A key area to concentrate on for cost control and reduction is a measure of direct costs associated with production.
Here are four key reasons why this cost analysis is essential.
1. Evaluating cost efficiency
Breaking down the direct expenses of raw materials and labor helps organizations identify which production components cost more than anticipated. It enables management to make informed decisions, optimize resource allocation, and eliminate wasteful practices.
2. Pricing decisions and profitability analysis
If the selling price of a product does not adequately cover its prime cost, the company risks operating at a loss. Businesses can set competitive and profitable pricing strategies by analyzing the costs.
Moreover, the analysis provides insights into each item’s contribution margin (selling price minus prime cost).
3. Identifying cost reduction opportunities
Prime cost analysis lets companies pinpoint areas where direct expenses can be minimized without compromising product quality or customer satisfaction. It helps negotiate better deals with suppliers for raw materials and optimize labor utilization.
4. Comparing prime costs across products or services
You can identify which products or services are more cost-effective and which need optimization. Comparing the prime costs across different offerings helps you drive these insights.
The insights influence strategic decisions, such as resource allocation, product mix adjustments, and investment prioritization.
Read More: What are Non-operating Expenses? – Definition, Calculation and Examples
Prime cost vs. conversion cost
Conversion costs are the expenses incurred during production to transform raw materials into finished products. In cost accounting, they determine the value of ending inventory on the balance sheet and help calculate the incremental cost of creating a product for pricing purposes.
Conversion costs establish the minimum selling price needed to cover all associated expenses when combined with component costs.
Differentiating prime cost from conversion cost
Aspect |
Prime costs |
Conversion costs |
Meaning |
Prime costs are the costs directly related to manufacturing goods. |
Conversion costs are the costs required to transform raw materials into finished goods. |
Formula/Inclusions |
Prime costs comprise direct materials and direct labor costs. |
Conversion costs include direct labor and all manufacturing overheads. |
Traceability to the final product |
Prime costs are directly traceable to specific products manufactured. |
Conversion costs are overhead components that cannot be directly traced to a particular product. |
Understanding the relationship between prime cost and conversion cost
Conversion costs comprise all manufacturing expenses except raw materials. In cases where a business incurs unusual conversion costs during a specific production run (e.g., reworking parts due to incorrect tolerances on the first pass), it may be reasonable to exclude these additional costs from the conversion cost calculation.
This exclusion is based on the consideration that such costs are not representative of day-to-day cost levels.
The calculation of conversion costs involves labor and manufacturing overhead:
Conversion costs = Direct labor + manufacturing overhead
Suggested Read: 10 Best Financial Management Tools for CFOs
Applications of prime cost in industries
Below are some notable industries where calculating or estimating prime cost is common.
1. Manufacturing
Prime cost assists in determining the actual cost of production by considering direct material and labor expenses. Manufacturing businesses must ensure the selling price covers these costs to make profits.
An analysis of the figures also helps control costs, assisting manufacturers in identifying areas where they can optimize resources and reduce expenses. Additionally, it’s instrumental in inventory valuation, as it helps determine the value of raw materials and work-in-progress inventory.
2. Food and beverage (F&B)
In the F&B industry, these costs are paramount for restaurant owners and managers. They can accurately calculate the prime cost per dish by analyzing the direct costs of ingredients (direct materials) and labor required to prepare dishes (direct labor).
It enables them to establish competitive yet profitable menu prices. Businesses can enhance their financial performance using prime cost analysis without compromising food quality.
3. Service
For service providers, this cost involves calculating direct labor costs associated with the delivery of each service. It includes wages, benefits, and any other directly attributable labor expenses.
With an analysis of prime costs, service-oriented businesses can determine appropriate service charges to ensure profitability. It also helps control costs, enabling companies to manage labor costs.
Quick Read: Selling Expenses: Types, Example and Calculation
Challenges in managing and calculating prime cost
Managing and calculating prime costs can present several challenges for businesses. Here are the significant hurdles they may face:
- Accurate allocation. Accurate direct material, labor, and expense allocation to specific products can be challenging, especially in complex manufacturing processes. Tracking raw material usage and labor hours becomes intricate, particularly when products share resources or go through multiple production stages.
- Fluctuating input costs. It impacts the calculations. Global economic factors, supply chain disruptions, and changes in market demand can lead to volatile prices for essential inputs. Managing these fluctuations in calculations requires constant monitoring and timely updates.
- Overhead allocation. Calculating and assigning factory overhead costs to individual products is complex, especially when overhead expenses are shared across multiple products or services. Deciding on an appropriate allocation method is crucial, as it can significantly impact the final figures.
- Data accuracy and timeliness. Prime cost calculations rely on accurate and up-to-date data from various sources, such as inventory records, time-tracking systems, and financial reports. Inaccurate data can lead to calculation errors, resulting in flawed pricing decisions and financial planning.
Read More: TOP 10 Financial Planning Tools That Accelerate Growth
Strategies for effective prime cost management
A cost management strategy helps set appropriate prices for goods and services, ensuring profitable business transactions. Effective prime cost management facilitates better project implementation, monitoring, and control, reducing cost overruns and wastage.
Strategies for effective management of these costs.
- Align with project strategy to make the foundation of any cost management strategy. Collaborate with team members, project managers, and subject matter experts to define project goals, scope, milestones, and budget. Ensuring the cost management strategy complements the project’s strategic vision enhances its effectiveness.
- A clear work breakdown structure enhances task-based project implementation. Divide the project into sub-parts, assigning specific tasks with defined timelines, required workforce, and scheduled deliveries. A detailed work breakdown facilitates resource and budget planning.
- Conducting strategic resource planning is a must before undertaking any project or business. Determine how task allocation will occur, minimize costs, assess the necessary budget, and evaluate the need for hiring freelancers or additional resources. Efficient resource planning optimizes cost management outcomes.
- Integrate risk management into the cost management strategy. Conduct a thorough risk analysis to improve decision-making and address potential project challenges. Anticipating and planning for unforeseen situations allows for more effective cost control and budget planning.
- Plan for contingencies for unexpected events by setting aside funds for emergencies. Having a reserve budget allows the organization to handle unforeseen circumstances, such as risky business decisions, project shutdowns, or unexpected disasters, without significantly impacting the overall financial stability.
Quick Read: Best Free Accounting Software in 2023
Bottom line
Prime cost is pivotal to calculating a product’s minimum sales price. A positive contribution margin suggests sales and production generate profits, whereas a negative contribution margin indicates the opposite.
Overall, the prime cost data help business owners determine lucrative goods and services. They can also use it to improve supplier negotiations and lower production expenses. Use the best practices mentioned in this article to make prime cost management more effective in your organization.
FAQs
Prime cost includes only direct expenses. Examples of these costs include expenses on raw materials and direct labor. In contrast, total production cost encompasses all costs incurred in the production process, including direct expenses and factory overhead costs.
Prime cost is essential in cost analysis and decision-making as it represents the direct expenses incurred in production. It allows businesses to assess their profitability accurately, set competitive prices, and make informed decisions about resource allocation and cost control.
Yes, prime cost can help determine product pricing by providing insights into the direct expenses involved in production, allowing businesses to set competitive prices that ensure profitability and sustainability.
The relationship between prime cost and profitability is that it directly impacts profitability by influencing the overall cost of goods sold and determining the margin between revenue and direct expenses, thereby affecting the company’s bottom line.
Prime cost analysis helps identify cost reduction opportunities by revealing specific areas of direct expenses, such as raw materials and direct labor, allowing businesses to target cost-saving measures and optimize production processes.
No, the prime cost can vary across industries depending on the nature of their production processes and the composition of direct expenses involved in manufacturing goods or providing services.
Yes, prime cost is used to compare the cost efficiency of different products or services. It represents the direct expenses involved in their production, enabling businesses to evaluate their relative cost-effectiveness.
Prime cost includes direct expenses like raw materials and direct labor, while conversion cost comprises direct labor and manufacturing overhead expenses, excluding raw materials.
Overhead costs impact prime cost analysis by increasing the total cost of production, thus influencing a product or service’s final profitability and pricing decisions.
Yes, seasonal businesses must consider fluctuating production volumes and direct expenses when calculating prime cost, as these variations can affect cost efficiency and pricing decisions.
The cost data for prime cost analysis should be highly accurate and reliable to ensure precise evaluation of direct expenses and informed decision-making.
Yes, prime cost analysis can be used in service-based industries by considering direct expenses related to delivering services, such as labor and materials, to assess cost efficiency and pricing strategies.
Prime cost impacts make-or-buy decisions by comparing the cost of producing a product in-house (direct materials and direct labor) with the cost of outsourcing or buying it from external suppliers, influencing the most cost-effective option.
Yes, prime cost can help assess the profitability of different product lines by comparing direct expenses to revenue, providing insights into their cost-effectiveness.
Yes, there are industry benchmarks and standards for the prime cost that can help businesses compare their direct expenses to industry averages and best practices.
Yes, prime cost can fluctuate over time due to changes in raw material prices, labor wages, production processes, and other factors affecting direct expenses.
Discussion about this post